RotaCut®: Significantly reduced energy costs for mixing
Case Study: Duderstadt biogas plant
Problem
High energy requirements for mixing the digester in the Duderstadt biogas plant
Solution
Vogelsang RotaCut pro
The customer and the problem
The Duderstadt biogas plant is designed to operate on dry digestion. The plant consists of a 2000 m3 digester, post-treatment tank and end store, and has a nominal power of 680 kW. Approx. 50% corn silage, 30-40% cow manure, 8% grass silage and 5% green cereal and grain are used.
With a dry substance content of 12-13%, the mixers in the digester soon reached full capacity and had a power requirement of 50kW. In order to compensate for this, it was decided that the digester should be circulated once a week with an existing rotary lobe pump.
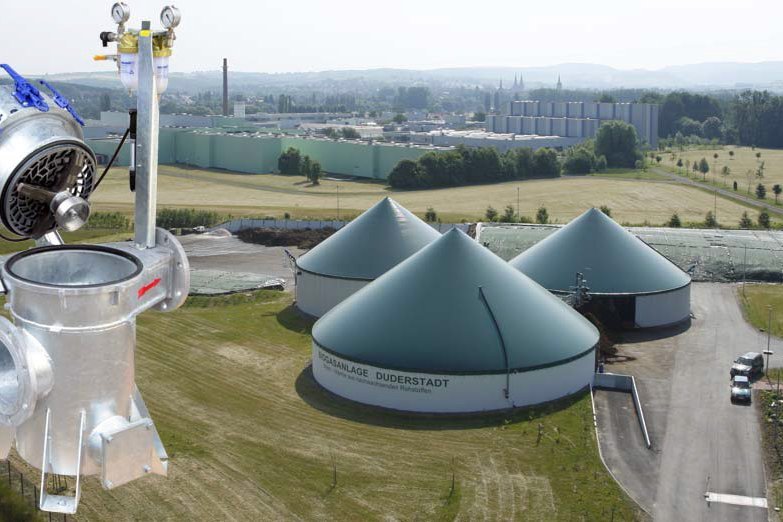
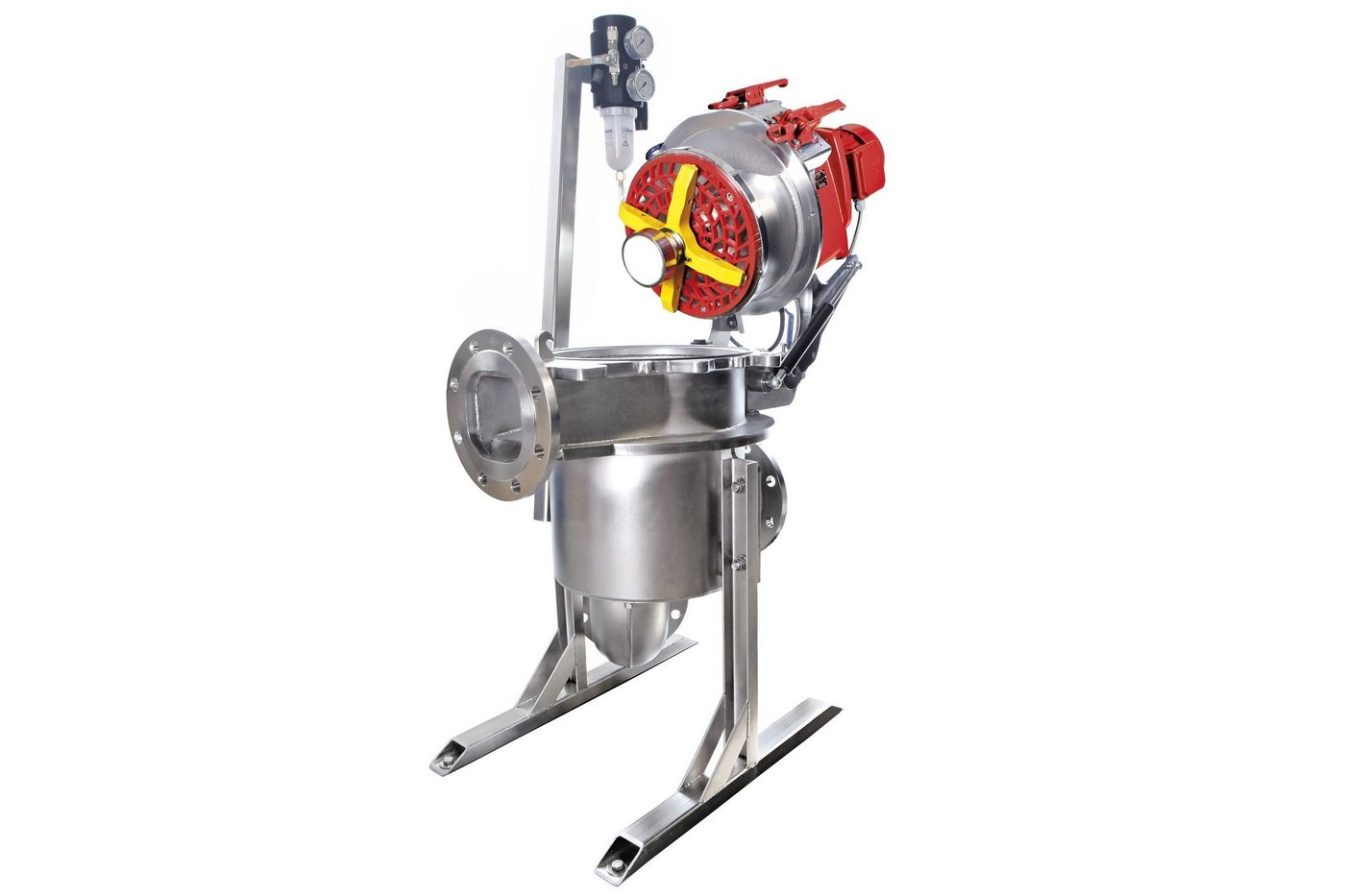
The solution
In order to protect against foreign matter whilst simultaneously treating the substrates, a RotaCut 5000 pro was installed.
This measure provided the breakthrough. Every weekend, the digester is circulated for approx. 60 hours. The combined power requirement of the rotary lobe pump and the RotaCut during this process is 10 kW. The power requirement of the mixers, on the other hand, dropped drastically to 30 kW at a running time of 40 minutes per hour. All in all, this means an energy saving of over 1,600 kWh per week / 85,000 kWh per year or – depending on the region – 10,000 - 12,000 euros per year.
With this massive improvement, the entire investment has paid for itself within a few months, and the biogas plant is now saving huge amounts of money.
Advantages of the RotaCut®
- Reliable maceration of fibrous and coarse material
- Protection against foreign objects for all downstream plant components
- Substrate more homogenous and flowable, allowing reductions in mixer power consumption