RedUnit: Treatment of poultry slaughter waste for the production of pet food
Case Study: Consorzio Gatteo Proteine
Problem
High maintenance costs and energy consumption
Solution
RedUnit XRL186-520QD drop-in installation
The customer
The treated material: poultry slaughter waste
The Consorzio Gatteo Proteine provides for the transformation of poultry slaughter by-products for the production of pet food. It was created with the aim of ensuring synergetic management in the delivery of their SOA production waste between the associated agri-food cooperatives, which represent almost all of the Italian poultry slaughter sector.
The production plant, located in Gatteo (Forlì-Cesena), uses advanced process technology that allows the total recovery of slaughter waste of poultry origin, producing animal flours for pet food.
The poultry slaughter scraps are delivered to the consortium through a logistics transport system that allows a continuous process 24 hours a day, 6 days a week. This waste is received inside a storage tank, inside a dedicated room, in compliance with the relevant hygiene and environmental regulations (extraction and purification of the internal atmosphere, etc.). Through a conveyor belt this material is sent to a shredding process, with a constant flow rate of about 10-12 tons/hour. A shredding operation is carried out at a lower size to be then more efficiently treated in subsequent steps; the shredded material is then sent to cooking processes (for fats), separation and drying, from which animal flours are obtained as a final product. Inside the plant there is also a "blood" treatment system from which substances are recovered and then used for the chemical and pharmaceutical fields. Our technological solution is located in the "shredding" sector.
The problem
The shredding system installed before RedUnit
The plant layout of the "shredding" compartment present before the installation of the Vogelsang RedUnit provided for the presence of a coarse sieve, that is a coarse single-shaft shredder, with a power of about 35.0 kW, inside which the material underwent a first "roughing". Subsequently, always through the use of a conveyor belt, it was first passed inside a metal detector (to remove any residual metal pieces) and then inside 2 finer shredders (classic mill shredders), which work in parallel (one in redundancy to the other, except in cases of peak input material (20 t/h) of 36.0 kW each. Finally, the crushed material was pumped into a cooker and then sent to the next steps, which involved the following problems:
- Installed power and very high consumption
- Suboptimal working efficiency (non-versatile system reactive to the presence of foreign bodies)
- More complex system to manage (also at the level of automation and alarm control)
- Constant maintenance and high working time costs (maintenance required at least 5-10 hours of work per week with the presence of 1 or 2 operators)
The system was therefore not optimal and functional for working needs and created various operational and economic problems.
The solution
The two RedUnit XRL 186-520QD installed in parallel
The installation of the Vogelsang RedUnit, with a power of 18.5 kW, made it possible to eliminate both the initial coarse shredder and the two subsequent finer shredders, conveying the entire material inside two XRL 186-520QD shredders, mounted in parallel to guarantee redundancy and to satisfy peak flow rates (20 tons/h). It is a double-shaft shredder composed of two monolithic rotors obtained from the solid, coupled to an in-line motor. Everything is controlled by a management and control panel that has been interfaced with the master PLC of the system, allowing direct communication in a totally interconnected system.
The installed power is thus lower and the data on consumption after commissioning is very interesting: with the previous solution there was a daily energy consumption of the shredding compartment of about 650 kWh, while now the energy consumption has been reduced to 250 kWh.
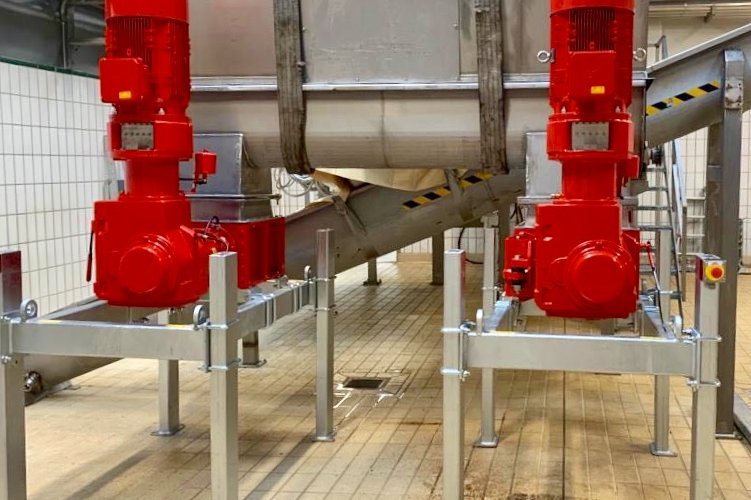
Despite the installed power not being high, the torque is transferred uniformly directly from the shafts to the rotors themselves, generating a very high shredding capacity; the instantaneous rotation inversion allows any blockages due to the presence of foreign bodies to be withstood; in addition the presence of breakage pins acts as a safeguard to the engine; the result: in a year of use no maintenance intervention was necessary on the machines.
Advantages of the RedUnit
- Reliable, defined shredding of tough material
- Individual assembly and configuration of the system components
- Plug and Play concept for quick and easy integration into existing plants
- Easy to control thanks to intelligent control unit and intuitive touch screen
- Easy to service for high availability
Benefits for the user
- Reduced electricity consumption
- More efficient and responsive system to foreign bodies
- Reduction of time and maintenance costs
- Optimal working efficiency
- Improved management of the entire system at the automation level
- Simple installation, retrospectively