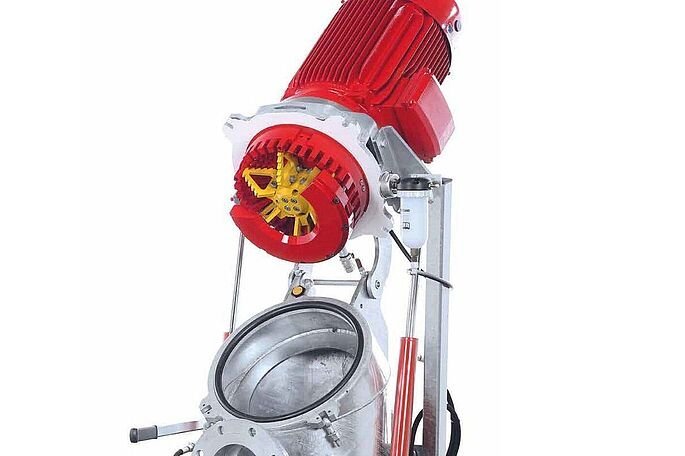
More efficiency through mechanical disintegration
DisRuptor
- Increases the surface of the biomass feed
- Homogenizes and reduces the viscosity of the organic suspension
- Accelerates and increases gas production
- Reduces the power consumption of mixers and pumps
- Easy to retrofit
Outstanding flexibility
The individually adaptable DisRuptor for mechanical disintegration of solid matter
Optimal substrate disintegration is key for determining biogas yield. This is why Vogelsang also offers a mechanical alternative or disintegrating substrates: the new, flexibly designed DisRuptor. The reduction of the particle size and the simultaneous defibering increases the surface area of the solid matter used. This helps bacteria reach the nutrients better, accelerates conversion and increases the gas yield.
The DisRuptor functional unit consists of a rotor with six blades as well as an outer DisRuptor ring. At high rotor speeds, the solid matter in the suspension is milled and frayed in the narrow gap between the rotor unit and the external ring. The gap can be individually adjusted to the specific application and the substrate. Thanks to these unique features, the DisRuptor offers particularly flexible and efficient mechanical treatment.
Mechanical disintegration with variable function unit
Mechanical disintegration system DisRuptor DR7000
The DisRuptor DR7000 offers energy-efficient mechanical disintegration thanks to its variable function unit. The handling of the adjustment mechanism is simple. The DisRuptor head is easy to swivel upwards with hydraulic support – offering direct access to the function unit. The gap between the blades and the external ring can be adapted individually to every substrate with just a few steps and without special tools. Moreover, wear on the ring and wings can be compensated for by realignment – extending their service lives.
Downloads
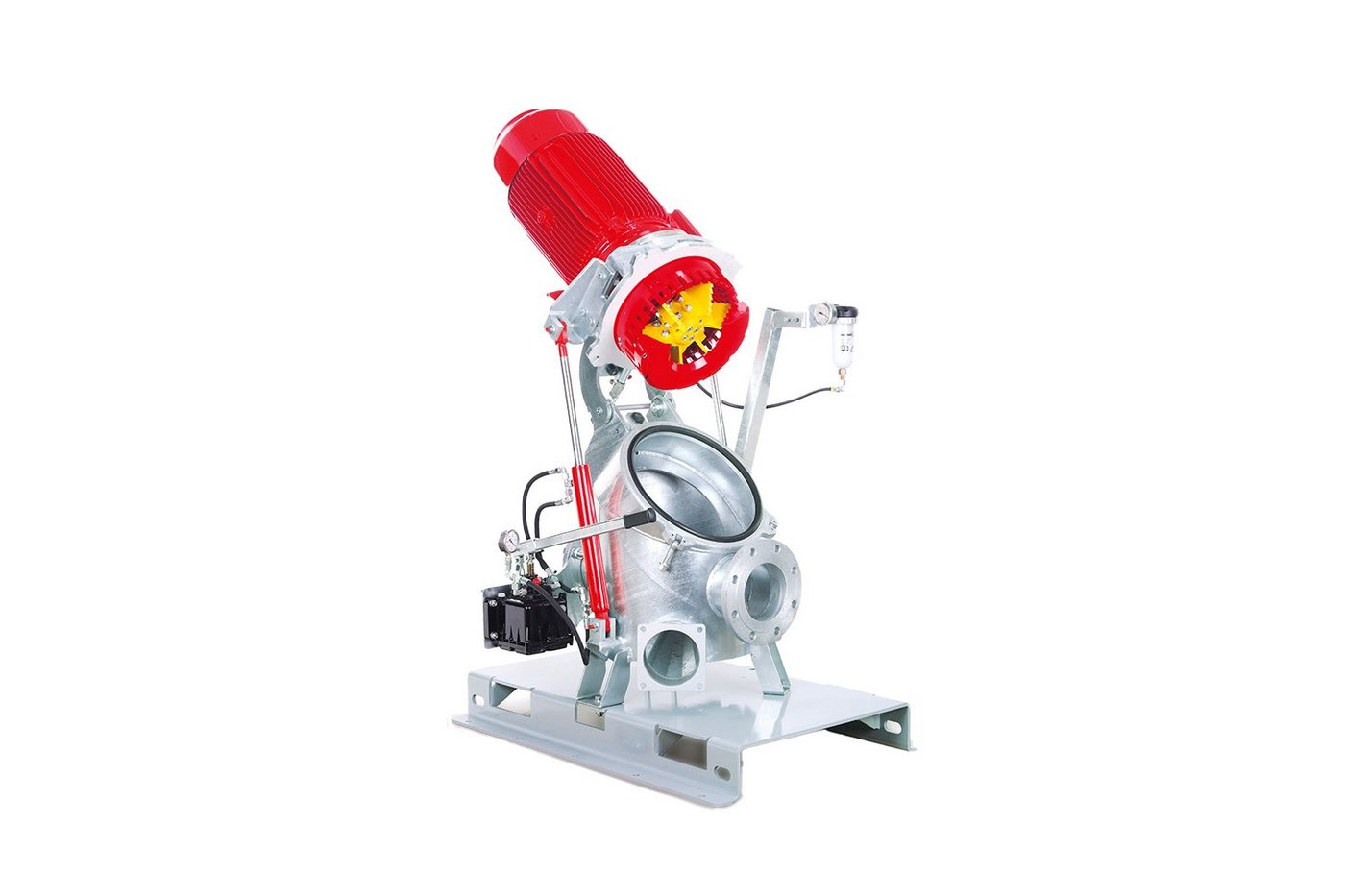
Mechanical disintegration with variable function unit
Mechanical disintegration system DisRuptor DR7000
The DisRuptor DR7000 offers energy-efficient mechanical disintegration thanks to its variable function unit. The handling of the adjustment mechanism is simple. The DisRuptor head is easy to swivel upwards with hydraulic support – offering direct access to the function unit. The gap between the blades and the external ring can be adapted individually to every substrate with just a few steps and without special tools. Moreover, wear on the ring and wings can be compensated for by realignment – extending their service lives.
Downloads
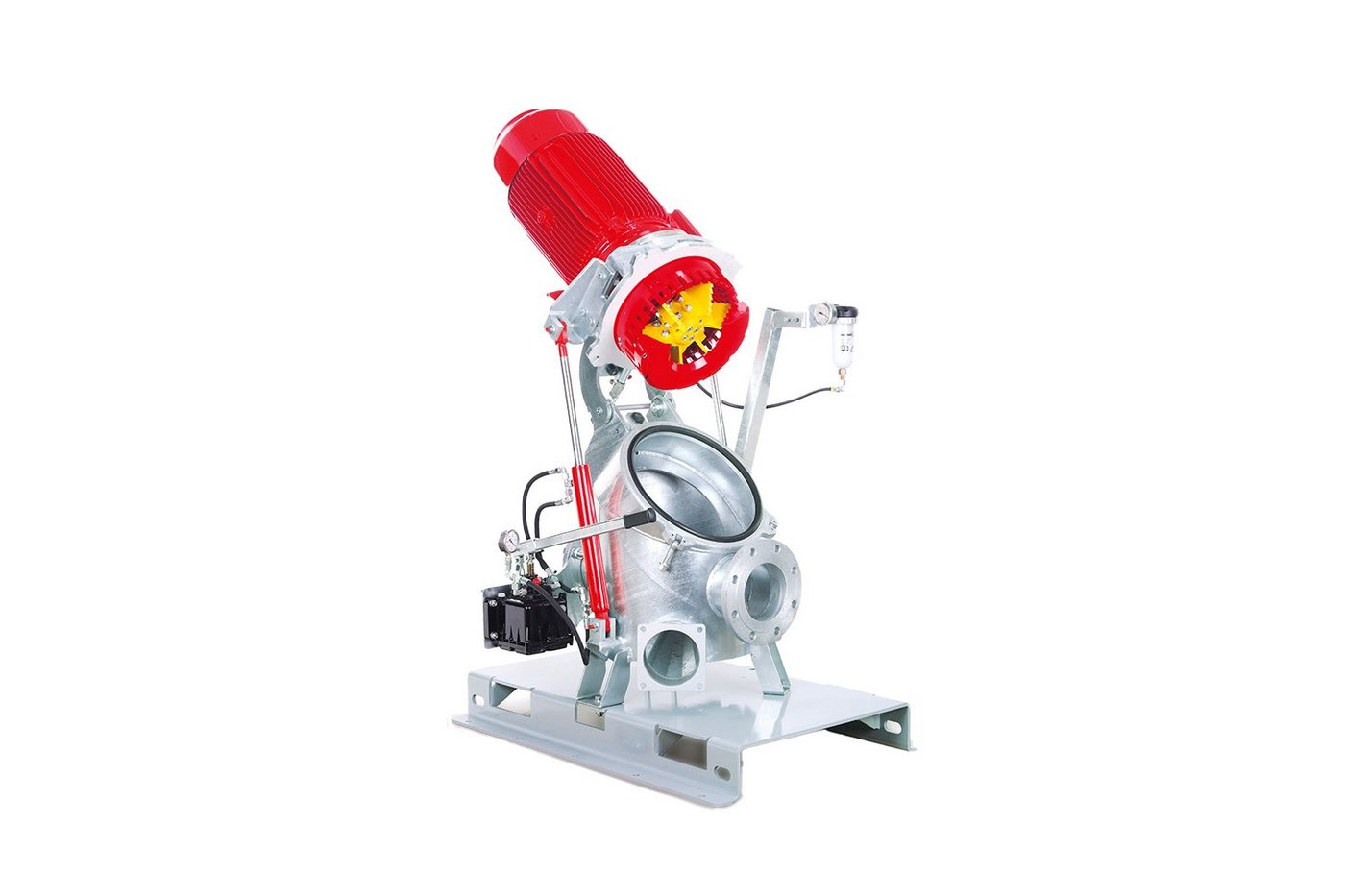
Features of the DisRuptor
Options of the DisRuptor
More on the product
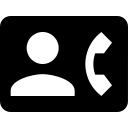
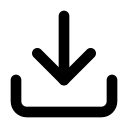
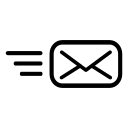